トライボロジー試験(摩擦・摩耗試験)
トライボロジー試験(摩擦・摩耗試験)とは
トライボロジーとは、摩擦、摩耗、潤滑、表面・接触に関する科学技術であり、物体同士が接触し相互作用を起こす際に生じる現象を研究する学問分野です。自動車、航空機、鉄道、船舶、医療機器、機械工学、材料工学、生物学、地球科学など、様々な分野で重要な役割を果たしています。
トライボロジーにおける研究成果(例えば、摩擦摩耗試験や表面性状解析の結果の応用)は、製品の信頼性向上、コスト削減・品質向上、安全性確保、省資源・省エネルギーにつながる材料、潤滑油、表面テクスチャ技術の開発、設計、適正選定などに役立てられています。
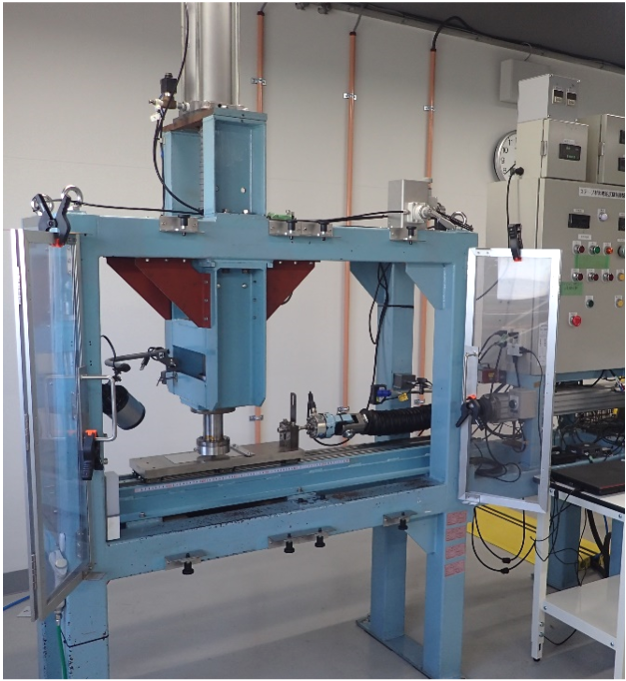
トライボロジーの技術分野
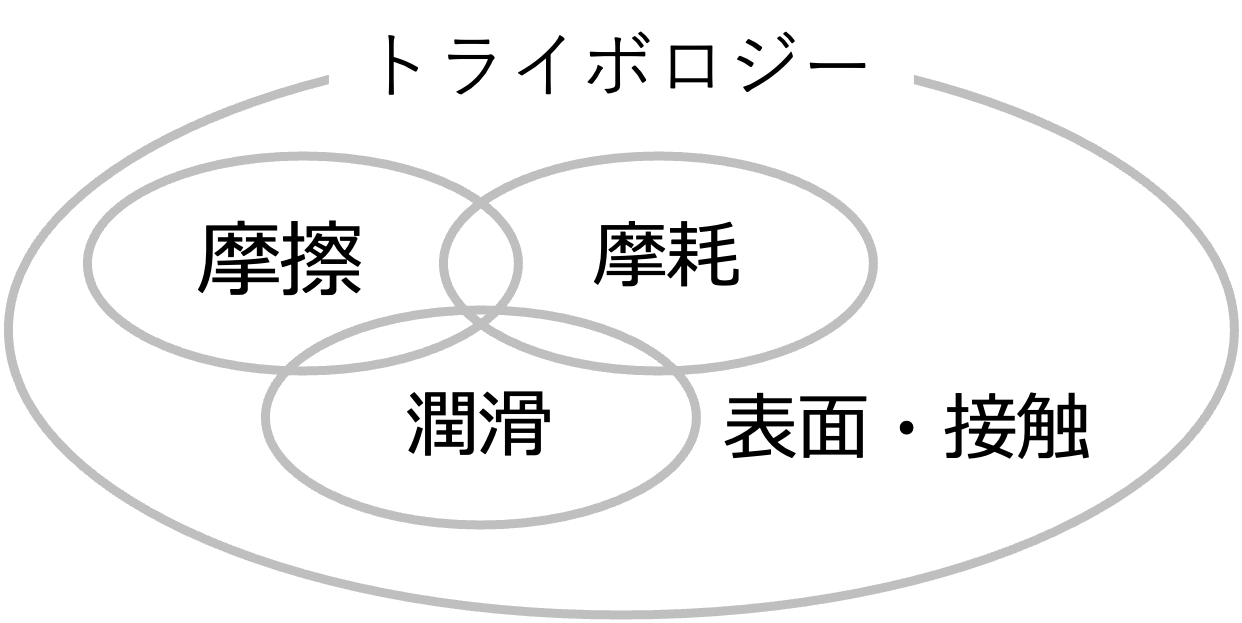
1.摩擦・摩耗試験
摩擦摩耗試験においては、実際の摩耗形態(凝着摩耗、アブレシブ摩耗、疲労摩耗、エロージョン摩耗、腐食摩耗など)や摺動環境(材料の組み合わせ、接触形態、雰囲気、面圧、摺動速度、温度、粗さ、表面処理、潤滑など)に合わせた試験方法を選択することが重要です。
当社は、20年以上にわたり摩擦摩耗の受託試験を行っており、その知識と経験を活かして、お客様の課題解決をお手伝いしています。また、設備面でも、スタンダード機に加えて、当社独自に開発した試験機や、近年世界各国の研究機関でも導入が進んでいる多機能型試験機を保有しています。これらにより、幅広いお客様のニーズに対応できる体制を整えています。
(1)往復摺動試験(ボールオンプレート、ピンオンプレート、ブロックオンプレート)
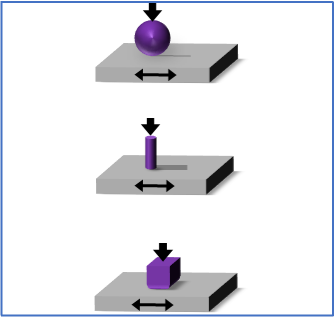
主仕様 *条件範囲は試験機により異なる
・荷重 0.1~5000N
・速度 0.1~80Hz、1~300mm/s
・温度 低温–40°C、高温500°C
・距離 1~250mm
・潤滑 ドライ、塗布、滴下、液中
事例
・摩擦係数の取得
・高硬度材(金型材、コーティング材)の摩耗
・フレッティング摩耗(接触電気抵抗)
・焼付き性
・潤滑性(オイル、グリス、水)
・引っかき抵抗
・ケーブルの摩耗
適用規格
・ASTM G133
・ASTM G181 等
(2)回転摺動試験(ボールオンディスク、ピンオンディスク、リングオンディスク)
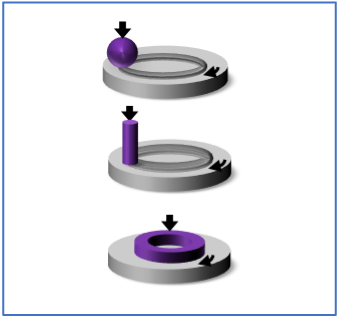
主仕様 *条件範囲は試験機により異なる
・荷重 0.1~5000N
・回転数 0.1~5000rpm
・温度 RT~1000°C
・潤滑 ドライ、塗布、滴下、液中
事例
・硬質膜(Crメッキ、DLC)
・樹脂 ・高温材料
・ストライベック曲線の取得
・表面処理材
・高速摺動性
適用規格
・ASTM G99
・ISO 18535
・JIS R1613 等
(3)ブロックオンリング試験
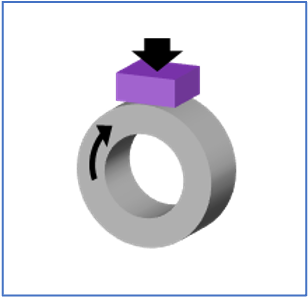
主仕様
・荷重 0.1~5000N
・回転数 0.1~3000rpm
・温度 RT~150°C
・潤滑 ドライ、滴下、下部浸漬
事例
・掻き上げ潤滑
・グリースの焼付き性
・ベアリング(ラジアル荷重)
適用規格
・ASTM G77
・JASO M358 等
(4)アブレシブ摩耗試験
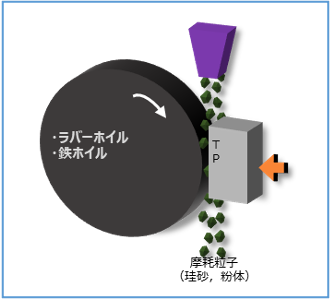
主仕様
・荷重 50~200N
・回転数 50~300rpm
・温度 常温
・粒子 珪砂、粉体 等
・潤滑 ドライ
事例
・耐摩耗材
・溶射材
・硬化肉盛り材
・建機材
・土砂摩耗
・摩耗粒子
適用規格
・ASTM G65
(5)スラスト転動疲労試験
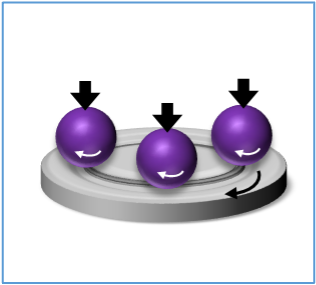
主仕様
・荷重 ~10kN
・回転数 ~3000rpm
・潤滑 液中
事例
・剥離評価(ピッチング、フレーキング)
・軸受鋼
・潤滑剤
・ベアリング
(6)2円筒試験試験(西原式)
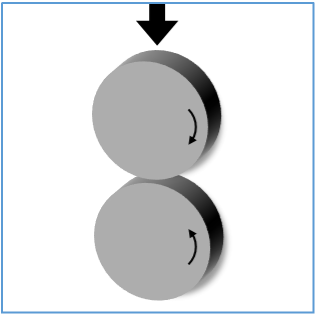
主仕様
・荷重 ~3000N
・回転数 ~800rpm
・潤滑 ドライ、滴下
・滑り率 3~30%
事例
・剥離評価(ピッチング、フレーキング)
・車輪材 ・レール材
(7)エロージョン試験
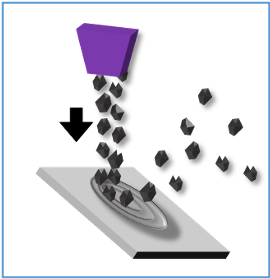
主仕様
・温度 RT~500°C
・衝突角度 30~90°
・潤滑 ドライ
・粒子 珪砂、スチールグリッド、粉体 等
事例
・配管材
・ライニング材
・耐摩耗材
・セラミックス
(8)スラリー摩耗試験
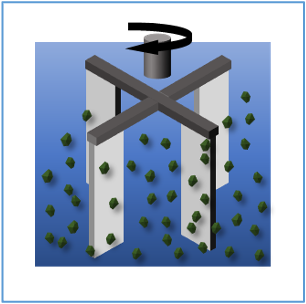
主仕様
・温度 10~60°C
・速度 ~7m/s
・濃度 ~50wt%
・スラリー 海水+砂 等
事例
・耐食材
・表面処理材
・フィルター材
・土砂摩耗
(9)ナノスクラッチ試験
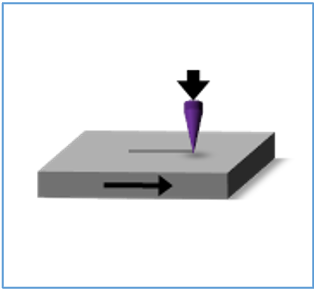
主仕様
・荷重 ~10mN
・X変位 ~15μm
・温度 RT~800°C
事例
・硬質薄膜(窒化珪素、DLC)の断面
・絶縁皮膜(電子部品)
2.表面性状解析(線粗さ・面粗さ)
表面性状とは、粗さ・うねり・表面凹凸・筋目・きず・外観など、表面の幾何学的性質の総称です。表面性状は大きくわけて以下の2種類の方式で評価します。
- 線(二次元)で表面凹凸を計測する「輪郭曲線方式(いわゆる“線粗さ”)」
- 面で表面凹凸を計測する「三次元方式(いわゆる“面粗さ”)」
従来の輪郭曲線方式とは測定条件・表面性状パラメータとその計算方法などが異なる「新しい輪郭曲線方式」のISOが2021年に制定されました。今後、この新しい方式がJIS規格化される予定です。
表1に評価方法と規格、弊社保有の測定装置を示します。当社では様々な測定装置を保有し、全ての規格に対応した表面性状評価が可能です。
表面性状測定装置
表1 表面性状の評価方式、規格、測定機(弊社保有)
評価方式 | 規格番号(表面性状パラメータ) | 測定装置 (弊社保有) | |
---|---|---|---|
ISO | JIS | ||
輪郭曲線方式 (線) | ISO 4287 : 1997, Amd. 1 : 2009 | JIS B 0601 : 2013 | 触針式表面粗さ測定機 |
新しい輪郭曲線方式 (線) | ISO 21920-2 : 2021 | JIS規格化予定 | 触針式表面粗さ測定機 走査型プローブ顕微鏡 白色干渉顕微鏡 共焦点顕微鏡 |
三次元 (面) | ISO 25178-2 : 2021 | JIS B 0681-2 : 2018 |
(1)輪郭曲線方式(線粗さ)の特徴
輪郭曲線方式は1ラインでの計測となります。そのため、単純な機械加工痕などの1方向に筋目のある表面の評価に適していますが、多方向に筋目のある表面やランダムな凹凸を有する表面を適切に評価することは困難です。
また、触針式表面粗さ測定機は探針の機械的な接触によって表面凹凸を計測するため、柔らかいサンプルや粘着性のあるサンプルの評価ができない、精密な位置決めが難しい、といったデメリットがあります。
(2)三次元方式(面粗さ)の特徴
三次元方式は面での計測となるため、輪郭曲線方式では評価困難な凹凸を有する表面も評価できます。さらに、凹凸の目の細かさや表面積、筋目の方向や方向性の強さなど、輪郭曲線方式では評価できない表面の特徴をパラメータとして数値化することができます。また、白色干渉顕微鏡や共焦点顕微鏡などの非接触測定装置を利用することで、表面状態や材質に左右されない評価が可能であり、顕微鏡像を見ながら正確な位置決めもできます。
三次元方式では、様々な測定装置が利用可能なことから、サンプルや評価目的に応じた、適切な水平/垂直分解能と測定レンジを有した装置の選択が重要です。また、パラメータの中には、測定データ間隔や形状・うねり・微小粗さ・ノイズ除去方法に影響を受けやすいものもあります。適切で再現性のある評価を行うためには、測定・解析条件の設定と開示が重要となります。
三次元表面性状評価例
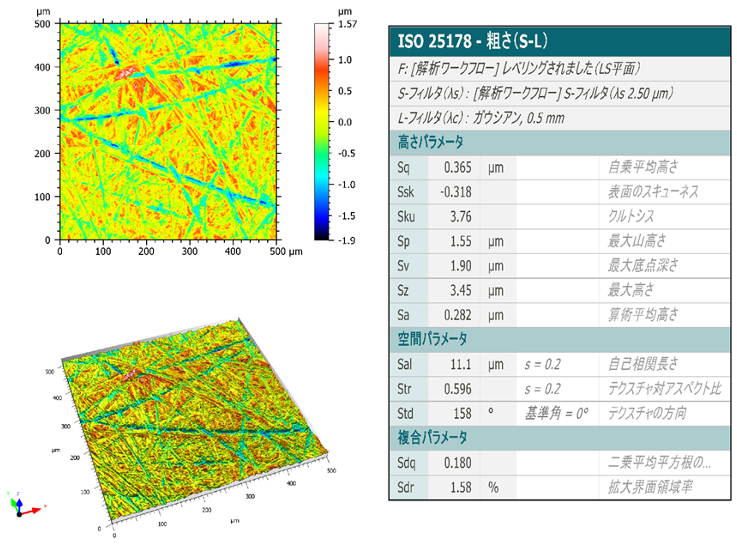
(左上)コンター図、(左下)3D図、(右)ISO25178 パラメータ
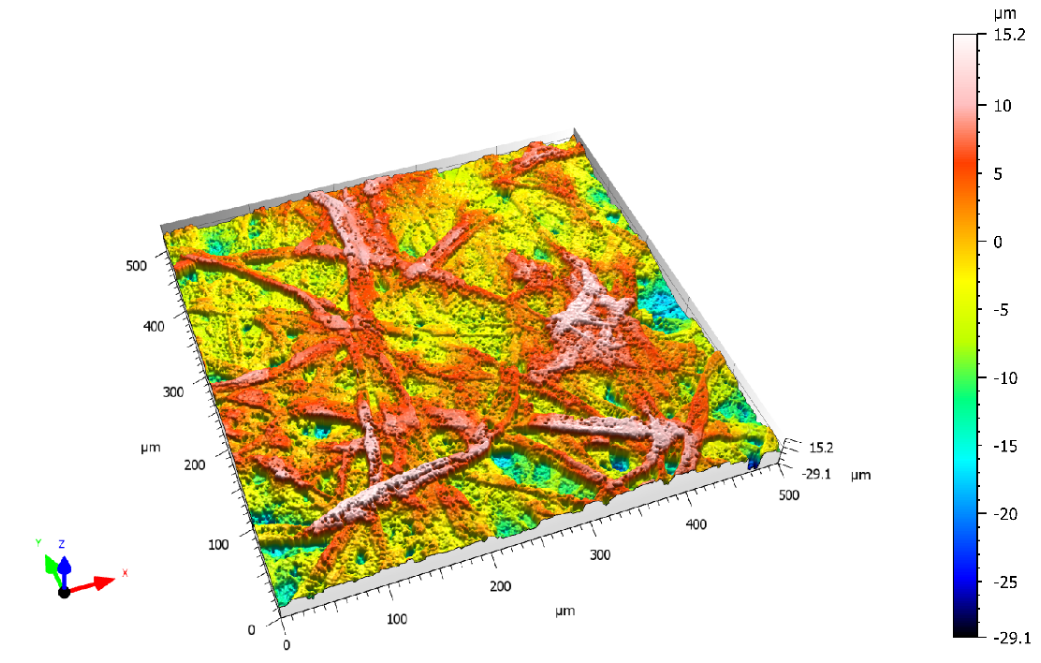
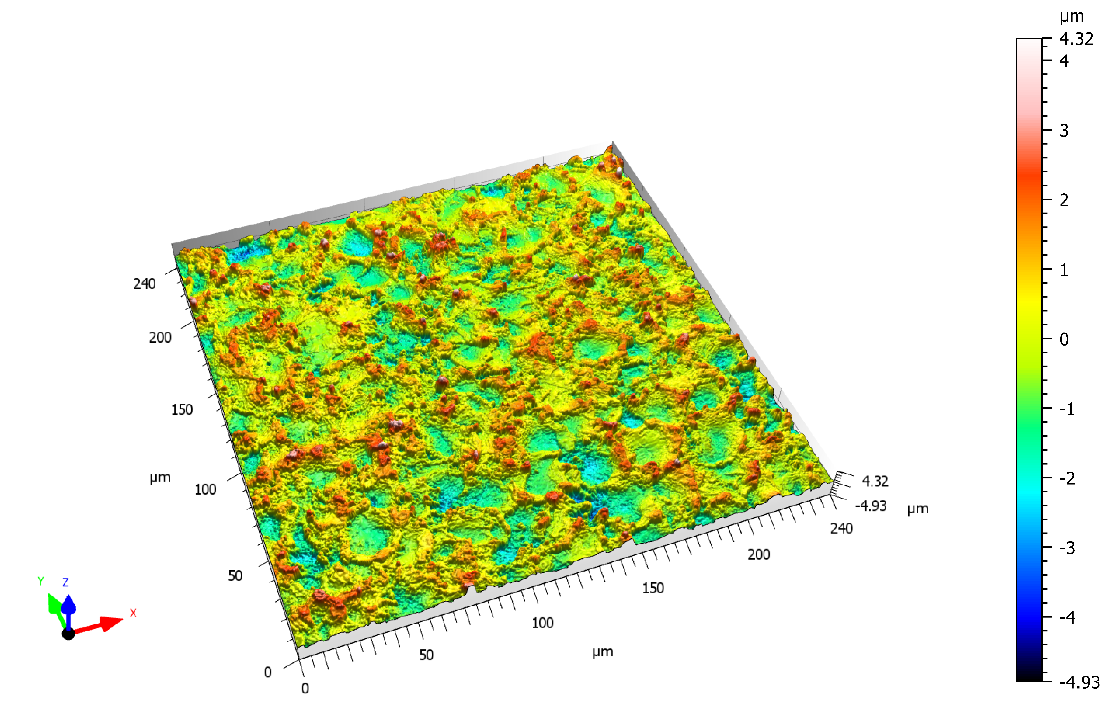
トライボロジーにおいては、表面性状パラメータは、接触状態(塑性接触・弾性接触)やストライベック曲線における油膜パラメータなどの評価に活用されます。また、摩擦摩耗試験前後の三次元表面形状データから、耐摩耗性の高い材料や、なじみ過程などにおける微小な摩耗体積を評価することもできます。