落錘(落重)試験
落錘(落重)試験とは
動的試験は、材料特性の速度依存性や部材の圧潰挙動を評価する試験で、当社は高速引張試験機や落錘(落重)試験装置、多機能衝突試験機を扱っています。
落錘(落重)試験は、錐体と呼ばれる重りを試験体の上に落下させ、衝突の破壊形態を模擬する試験で、部材の衝突吸収エネルギーの吸収特性や変形状況(変形モード、破断のタイミング等)の観察に用いられます。モデル試作品から実部品、モジュール単位での評価を様々な条件下で実施できるよう、治具を含めた試験のご提案をします。
当社は“落錘(落重)試験のトップランナー”を自負しており、その対象は、自動車の衝突安全性評価を中心に、衝撃影響評価の必要な多岐分野に広がっています。
落錘(落重)試験設備
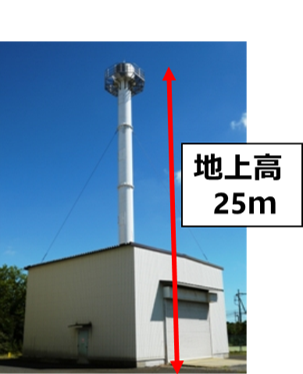
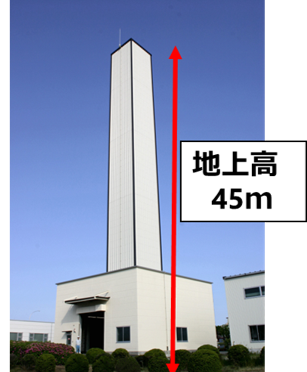
落錘(落重)試験の特徴
- 落錘試験では当社が世界のトップランナーです
- 2000年の初試験以来の約20年で、2万体近くの試験実績を積み重ねています
落錘(落重)試験の適用分野
自動車分野(衝突安全性評価、衝撃吸収部材設計)
- 部材(単体、ASSY)の強度・衝撃吸収性能(ex. センターピラーの設計、 バッテリーユニット含むフロア構造設計、etc.)
- CAE結果の検証
- 衝撃荷重の分布把握(ex. 軽量化ターゲット(強度部材)の絞り込み、etc.)
鉄道、船舶、建築・土木構造物
- 衝撃力の影響評価(ex. 連結器、水圧衝撃や地震衝撃の模擬、etc.)
- 衝撃吸収性能評価(ex. 排障器設計、衝撃吸収構造体設計、etc.)
落錘(落重)試験の原理
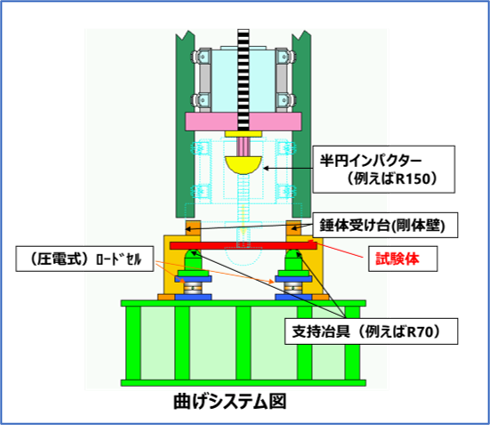
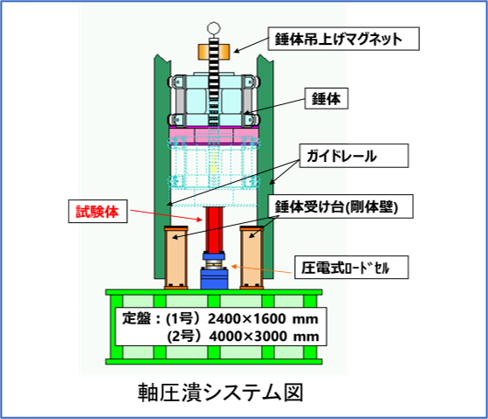
電磁石で持ち上げた“おもり”(錘体)を所定の高さで電磁石から切り離し、衝突試験体を変形させ、その荷重や変形挙動を把握します。錘体の変位Sはレーザー等の適切な方法で測定し、変形時の荷重Fはロードセルにより測定することにより、荷重変位線図(FS線図)が得られます。また高速ビデオ撮影により、試験体の変形挙動を観察できます。
- 1)部材表面の歪挙動は、DIC(デジタル画像相関法)により可視化できます
- 2)歪ゲージ、加速度計、モーションキャプチャー等の計測器も併用できます
- 3)錘体は自由落下するため、その速度は高さのみに依存します(空気抵抗は無視)
- 4)錘体の衝突部形状は任意に設定出来ます
- 5)実現象を模擬する衝突条件は、適切な治具設計と併せて提案します
落錘(落重)試験装置の主な仕様
| 波崎1号機 | 波崎2号機 |
最大落下長 | 16.5m | 35m |
---|---|---|
最大速度 | 64km/h | 94km/h |
錘体重量 | 1Ton | 3Ton |
筒内寸法 | Φ1.2m | □4m |
定盤寸法 | Max 4m×3m | |
錘体重量範囲 | 237~3,000kg | |
試験速度 | MAX 94km/h | |
荷重計測 | 1MN 圧電式 1軸ロードセル 1MN 歪ゲージ式 3軸ロードセル |
落錘(落重)試験の事例
事例1;自動車分野の様々な試験対象(代表例)
- 1)材料開発に関わる基本形状(ハット断面、多角形断面等)の部材を部材軸方向に圧潰し、動的圧潰性能を評価します。(写真a)
- 2)部品単体の衝撃エネルギー吸収性能を評価・比較します 。 (写真bはクラッシュボックス)
- 3)複数の部品から構成される部材 (部品アッセンブリー、ASSY)の衝撃エネルギー吸収性能を評価します。(写真cはフロントバンパー+クラッシュボックスの前面衝突対応部材)
- 4)自動車カットボディーを用いた衝突模擬試験(図dは後突模擬)
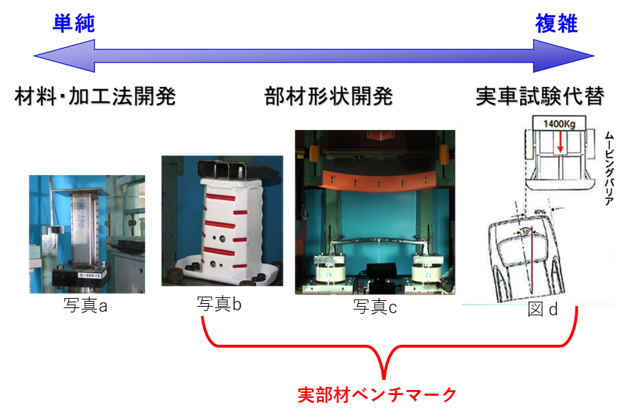
事例2;フロントアッセンブリーの前面衝突模擬試験
- 1)バンパー+クラッシュボックス+フロントフレームから構成されるアッセンブリー(自動車前面の右側部分モデル)による前面衝突の模擬試験です
- 2)アッセンブリーの各部品の衝撃吸収性能、圧潰形状、接合部を含めた破断状況等を把握できます
- 3)試験全容を実時間でのムービー動画から音も含めてご覧ください
- 4)高速ビデオによる動画により部材の圧潰状況が鮮明に観察できます
- 5)高速ビデオ画像とロードセルによる荷重-変位グラフ(FS線図)から圧潰状況を定量的に分析し、その改善策を考えることが出来ます
フロントアッセンブリーの衝突模擬試験(試験全容ムービー)
フロントアッセンブリーの衝突模擬試験(高速ビデオ)
◆高速ビデオ画像とFS線図からの解析
- 1)変位は錘体の鉛直移動距離でバンパーへ衝突接触した瞬間を0とします
- 2)衝突後荷重は上昇しクラッシュボックス圧潰が始まるとほぼ一定値を示します
- 3)Frフレーム圧壊が始まると荷重は急上昇しますが直ぐに座屈し荷重が抜けます
- 4)その後荷重は上昇しつつ圧潰が完了します
◆FS線図からの考察
- 1)FS線の下部の面積(薄ピンク色部分)は部材の衝撃吸収エネルギーを示します
- 2)Frフレームの想定外の座屈が無ければFS線は青線に近いものになるはずでした
- 3)座屈により衝撃吸収エネルギーは濃ピンク部分だけ低下したことになります
- 4)この座屈を防止し所期性能を得るため材料強度や部材形状の変更を案画し、次の試験で改善を確認する、といった過程を1,2回繰り返し部材設計は完了します
- 5)実部品の各種ばらつきも含めた設計が短期間かつ低コストで実施出来ます
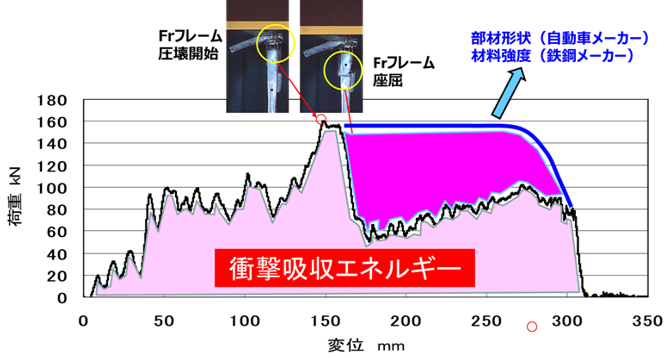
事例3;ホワイトボディーの米国ポール側面衝突模擬試験
- 1)米国IIHSの規則によるポール測突試験を落錘試験により実施した事例です
- 2)実車試験では車をポールへ向かい斜め15°時速32kmで衝突させます
- 3)落錘試験では車を幅方向を半分にカットして斜め15°で固定しポール形状の錘体を時速32kmで落として試験を実施します
- 4)この試験により衝突CAEの検証や、衝突対応骨格部材の開発優先順位決定(ターゲット部材の選定)等が出来ます
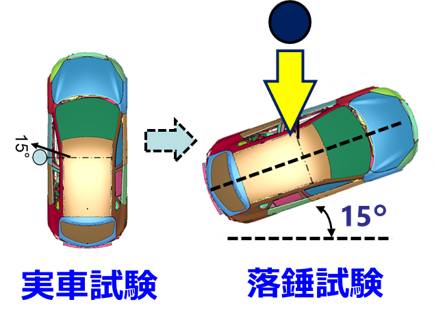
ホワイトボディーの側面衝突模擬試験(ムービー+高速ビデオ)
注) テストベッド寸法内のボディーに限り試験可能
落錘(落重)試験で得られる情報と適用例
1)部材(単体,部品アッセンブリー)の強度・衝撃吸収性能
- 部材の軸圧潰試験,曲げ圧潰試験 ⇒ 変位-荷重(FS)線図と圧潰挙動(高速ビデオ画像)
- センターピラー等の車両骨格部材(衝撃エネルギー吸収部材)の設計
- バッテリーユニットとその衝突対応部材を含むEVフロアの構造設計
2)CAE結果の検証
- 複合部材(鋼材,非鉄金属,樹脂等利用,バッテリー装着等)の接合部を含む圧潰結果
- 変形着目部材へのDIC(デジタル画像相関法)併用によるひずみ,応力の可視化
3)衝撃荷重の分布
- ホワイトボディー等のフルカー衝撃試験による軽量化ターゲット部材(強度部材)の絞り込み
⇒1.部材設計へ