化学的手法によるリチウムイオン電池の解体評価
RSM-2501
1.概要
リチウムイオン二次電池の長期信頼性を評価するには加速試験を行うことが有効です。当社では目的に応じた様々な信頼性試験の実施に加え、加速試験後の電池の中に残された情報を化学分析により数値化し、定量的に比較することが可能です.
評価に用いた誘導結合プラズマ質量分析法(ICP-MS)についてはこちらから
2.測定事例 【 高温保存試験後の解体評価 】
高温保存試験で異なる劣化状態(図1)が確認された試作セルを解体し、劣化に伴い正極から溶け出した微量元素(活物質・集電箔起因)の濃度をICP-MSで部材別に測定しました。
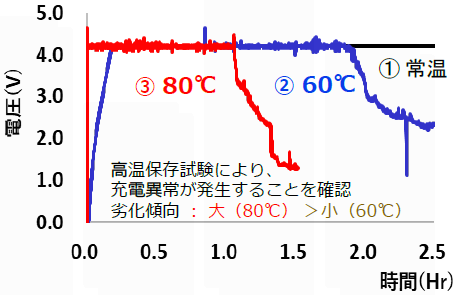
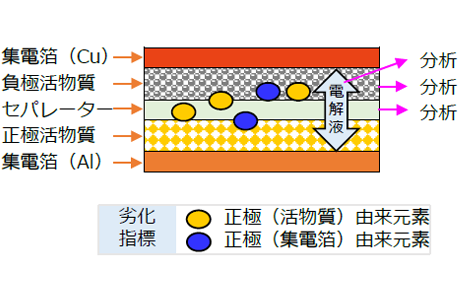
2.1 試作したラミネートセル
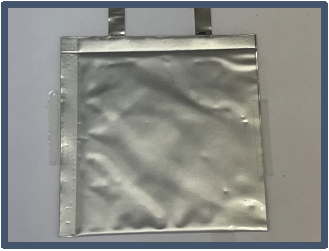
表1.ラミネートセルの構成
正極 | 活物質 | LCO(LiCoO2) |
バインダー | PVDF | |
導電助剤 | アセチレンブラック | |
集電箔 | アルミ箔 | |
負極 | 活物質 | 球晶黒鉛 |
バインダー | PVDF | |
集電箔 | 銅箔 | |
電解液 | EC:EMC(1MLiPF6) | |
形状 | 80×120mm |
2.2 高温保存試験による評価用ラミネートセルの作製
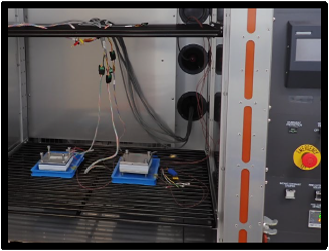
表2.セルの高温保存試験条件
保存温度(3条件) | 充電状態 | 保存期間 |
1)常温 2)60°C 3)80°C | SOC100% | 2週間 |
2.3 高温保存試験後の部材別成分分析結果
2.3.1 部材別のCoの測定結果
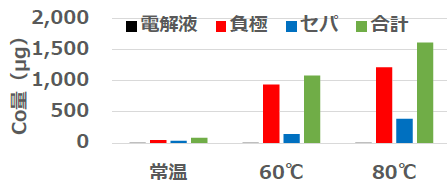
試験条件(2週間保持) | Co(μg) *正極活物質由来成分 | |||
電解液 | 負極 | セパレーター | 合計 | |
1.常温 | 1.26 | 48 | 36 | 85 |
2.60°C | 1.02 | 937 | 143 | 1081 |
3.80°C | 3.13 | 1219 | 392 | 1614 |
2.3.2 部材別のAlの測定結果
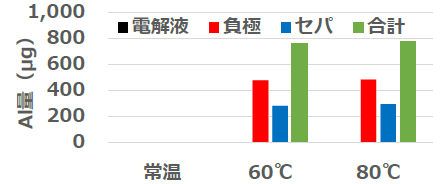
試験条件(2週間保持) | Al(μg)*正極集電箔由来成分 | |||
電解液 | 負極 | セパレーター | 合計 | |
1.常温 | 0.13 | 1 | 2 | 3 |
2.60°C | 1.36 | 479 | 282 | 762 |
3.80°C | 1.58 | 483 | 295 | 779 |
ICP-MSで測定した結果、Coの検出量は保持温度が高いほど増加することが確認されました。また正極箔由来のAlが検出されました。
検出箇所別では負極が最も多いことが判りました。
3.まとめ
3.1 セル内での反応と試験後に確認可能な項目
セル内での反応(推察) | 高温保存試験後に確認可能な現象と測定事例 |
---|---|
|
|
3.2 正極活物質(LiCoO2)の劣化イメージ
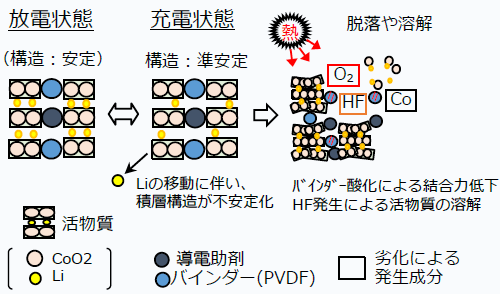
今回の試験では、試作セルを電池の動作環境としては高温である60°Cと80°Cに保持することにより、意図的にダメージを与えたセルを化学分析で評価しました。その結果、劣化指標の一つである正極活物質(本事例ではCo)の総溶出量は、保持温度が高いほど増加することが確認できました。
今回の事例では保持温度を変動要素として耐熱性を比較していますが、変動要素を変えることにより、異なる部材の良否などを定量的な指標で比較することが可能となります。